Meyer Sound Milestones
For more than 45 years, Meyer Sound has set the standard for sound reinforcement innovation. Scroll through the timeline to discover our history of product releases, awards and accolades from 1967 to the present.
"Everybody is very happy with the sound and headroom of the Acheron Designers. The speakers sold themselves!" says John Morris, supervising sound editor and sound designer, 20th Century Fox.
Meyer engineered the recording using the mid/side microphone technique invented by recording pioneer Alan Blumlein. suspending a single Neumann SM69 stereo microphone above and in front of the performers, then routing the signal into a custom tunable, complementary phase M/S matrix, and recording it on a Nagra D-II digital tape recorder at a 96 kHz sample rate and 24-bit resolution.
Meyer envisioned the next step for the technology as being that customers who purchase a system would receive a turnkey system, a complete package of design and tuning services from trained specialists in acoustics and digital audio, as well as hardware components designed specifically for the needs of electroacoustic architecture. The tuning process underwent transformation to increase its efficiency and methods. The result of this holistic upgrade was dubbed "Constellation" by Grammy-winning classical music recording and live sound engineer John Pellowe, who became involved in its development.
The first Constellation system was installed into Zellerbach Hall, on the University of California Berkeley campus. Meyer Sound had a long association with Zellerbach, and the timing was perfect, as Zellerbach faced an acoustical challenge in the variety of program material on the bill of their upcoming centennial gala.
The system made a characteristically low-profile debut at the gala in Zellerbach Hall on May 12, 2006 and received enthusiastic responses. Constellation was now officially launched.
Finally, around 2004, he decided the time had come and Meyer Sound embarked on a collaboration with LCS Audio, a small company making a powerful, high-quality digital audio system for theatrical sound, on a new, all-digital system drive processor. The project was headed by Perrin Meyer, John and Helen's son and the company's software R&D manager. In late 2005, the Galileo 616 processor and Compass control software for it shipped to an audio world eager to see what Meyer Sound would do in its first foray into digital audio.
The Galileo system was a breakthrough in a number of respects, including the number of inputs and outputs, its fixed latency, and its Composite EQ, which allowed corrective equalization with a minimum of phase shift.
The fact that one of the very first units was installed at Carnegie Hall underscored both the industry's confidence in Meyer Sound and its enthusiasm for Galileo's features and performance.
Meyer Sound collaborated with LCS Audio in the creation of the Galileo loudspeaker management system, during which time it became evident that both companies could benefit by joining forces: Meyer Sound would gain an established, experienced, forward-looking digital audio team for its new initiative into that field, while LCS Audio would gain the benefit of Meyer Sound's greater resources and highly successful vision and methods.
The two companies had many similarities in their corporate philosophies and cultures, and even overlapping markets, which made the idea even more attractive. In late 2005, Meyer Sound acquired LCS Audio and took the next step down the path Galileo had established.
There are several methods that are often tried for protecting against this. One is a standard limiter, but at the low frequencies of concern, they are often too slow when they need to be instantaneous. Further, very short attack times can sometimes produce artifacts. Another method is a high-pass filter, but they are not very effective and can introduce significant phase shifts that degrade the sound.
Frequency-dependent limiters are a third method that has been applied. The frequency-dependent limiter triggers limiting at different levels for different frequencies, in accordance with measurements of the loudspeaker taken during the development phase to determine the maximum allowable voltage at those frequencies. In most cases, these limiters were used in open loop systems (that is, without a controller receiving feedback from the loudspeaker) and, as a result, had to be quite complex, involving matched filters and other difficult circuitry.
This patent is for a greatly simplified circuit for a frequency-dependent limiter. Clever use of feed-forward and feedback circuits eliminates the need for matched filters. Other efficiencies are introduced by circuits that combine two functions that are separate in other frequency dependent excursion limiter designs. Overall, not only is the complexity of the circuit less, the parts count is also considerably reduced.
Also addressed in the patent is the use of the limiter in a closed-loop system such as Meyer Sound's self-powered loudspeakers.
MICA's QuickFly rigging introduced captive GuideALinks, which greatly improved safety by eliminating the need to ever put hands or fingers between cabinets, as well as providing the convenience of links that were permanently mounted in the rigging frame.
Meyer realized that similar sound reinforcement scenarios were not uncommon: large, primarily flat spaces that needed even coverage best accomplished with a distributed system, such as a convention center or a church. The MVC-5 is actually a small line array in a single enclosure, with the splay angles fixed to yield graded vertical coverage, through which level stayed fairly constant as one moved towards the loudspeaker.
The decision was made in Spring 2004 to proceed with construction….with a deadline of late October when the company wanted to show the theatre during the Audio Engineering Society convention in San Francisco, during which time it was also holding a celebration of the company's 25th anniversary. The race was on to get the theatre built, but it was complicated by constant adjustments to the design.
As the theatre is being designed and built, John Meyer formulates and puts into practice new ideas on the building of multipurpose spaces. Events of the time, such as Meyer Sound's participation in the "Mythbusters" TV show "Brown Note" episode, influenced aspects of the how the theatre is built.
In the nick of time, the beautiful 57-seat theatre is completed. The theatre's design and equipment are unique and, after the acquisition of LCS Audio in 2005, a VRAS system is installed, the first step in the formation of Constellation electroacoustic architecture. After the death of Don Pearson, the theatre is named the Pearson Theatre in his honor.
During the show's premiere season, "MythBusters" called on Meyer Sound Staff Scientist Dr. Roger Schwenke to confront the legend that a duck's quack doesn't echo. To debunk this myth, live duck quacks were recorded and analyzed in a meadow at a duck farm, in Meyer Sound's anechoic chamber, and in a large, empty warehouse.
Several months later the "MythBusters" team returned to Meyer Sound, recruiting both Schwenke and John Meyer to test a myth rather less suited to squeamish viewers: the so-called "Brown Note."
In yet another investigation, Schwenke was tapped a third time to help confront the myth that a wine glass can be broken by a singer producing the proper pitch. (It can.) This time, the "MythBusters" crew came to Meyer Sound's own Pearson Theatre to tape part of the sequence, which used a UPA-1P loudspeaker and a SIM 3 audio analyzer.
After prototyping several different approaches, the 700-HP ultrahigh-power subwoofer was released in late 2003. The 700-HP had truly massive output (139 dB SPL max) and enough headroom it was nearly impossible to clip, yet very low distortion. The market responded enthusiastically and immediately, and the 700-HP replicated the success the 650-P had received years before.
While the UPM-2P had won the hearts of the theatre community — and an EDDY award — for its brilliance in fill applications, the M1D and M2D did the same for main FOH systems, winning their own EDDY
The system described in the patent employs a microphone mounted in front of the low-frequency driver to acquire a pressure feedback signal from the drivers' audio output. This signal is then scaled and subtracted from the audio input signal (which is also scaled) to derive a difference signal. The difference signal is passed through a series of filters to generate a correction signal that is then applied to the loudspeaker.
By placing the microphone very close and off-axis to the speaker, the delay time in the feedback is minimized, room effects do not affect the servo mechanism and cone breakup mode effects at higher frequencies are minimized (simplifying the task of modeling the driver's behavior). The filter network generating the corrected signal can be implemented digitally or with analog circuitry.
The system offers advantages over other systems commonly applied to subwoofers in order to flatten response. One system applies an equalized signal to the driver, but the signal is fixed and is not derived from feedback on the system's operation, making it unable to compensate for modifying effects such as aging or environmental factors. Another system attaches an accelerometer to the voice coil, which adds mass to a critical component.
The Mars facility implements many simple, yet clever and effective ideas to streamline the assembly process while maintaining the extraordinary level of quality assurance for which Meyer Sound is known. The name followed in the tradition of planetary names established with the creation of the Saturn transducer fabrication facility.
The UPJ-1P employed a rotatable horn, an idea that others had done, but with one very simple and important improvement: the UPJ-1P's horn was marked to give a visual indication of which orientation had the wide coverage angle! The other major feature aimed at the installation market was a broad variety of mounting options, from pole mounting to small arrays.
The installation market loved the UPJ-1P from its release….as did the touring market, which finds the UPJ-1P ideal for fill applications.
Named for John and Helen Meyer's grandson, the MILO loudspeaker was much lighter than the M3D. It was also a four-way system, incorporating three two-inch diaphragm compression drivers dedicated to reproducing very high frequencies. The mid-high and very high-frequency sections used the latest versions of the patented REM manifold.
MILO was capable of very high output with low distortion and an extremely smooth, extended high-frequency response. It's QuickFly rigging was improved over the M3D rigging, but the cabinet was the same width so that it could easily be rigged with M3D-Sub directional subwoofers or M3D line array loudspeakers.
When the MILO was released, it took off like a rocket, winning both high sales and multiple awards. Though Meyer Sound's business was already on a strong upswing, MILO suddenly took things to another level altogether, starting a growth spurt that has yet to subside.
After a few years, some clever M1D owners realized that they could be used outside of arrays: individual cabinets worked excellently for frontfill or under-balcony coverage. This usage of the M1D has now become commonplace.
While the M3D is extremely powerful and full-range, with a frequency response that goes down to 35 Hz and all the way up to 18 kHz, the real breakthroughs it exhibited came in other areas, most notably in the form of BroadbandQ technology.
Loudspeaker specifications often state horizontal coverage angles, but the reality is that horizontal coverage varies radically with frequency across the response of a full-range loudspeaker. The M3D combined two Meyer Sound advances to produce a loudspeaker that maintains a much more consistent horizontal coverage angle across its wide response.
In the low end, the directional steering technology first developed in the PSW-6 is employed to yield a cardioid coverage pattern. For the mid and high frequencies the M3D introduced the patented REM manifold, which lets high-output compression drivers deliver the kind of directional control associated with line sources. Together, these two advances comprised BroadbandQ.
Second, MAPP Online used a patented method wherein a sound designer using an Internet-connected personal computer running Java-based client software creates a scenario for prediction, specifying a number of parameters.
Once the system parameters are defined, this information is sent over the Internet to a server at Meyer Sound headquarters in Berkeley, Calif. Running a sophisticated acoustical prediction algorithm, the server predicts the sound field that the loudspeakers will produce, as well as average and peak SPL and frequency and impulse responses at specified "virtual microphone" positions.
Within a few seconds, MAPP Online generates transmits the prediction results back to the local computer as a color graphical image.
MAPP Online was available free on request and equipped Meyer Sound users with a powerful tool that allowed them to design systems in advance with confidence that the real system would perform as the prediction indicated.
In 2006, MAPP Online Pro, the next generation of this ever-evolving software, replaced MAPP Online.
Fontana brought his problem to John Meyer, who was intrigued and set to work on a solution. The result was the MM-4, an incredible loudspeaker barely four inches on each side, yet with an operating frequency range from 120 Hz to 18 kHz and a maximum peak output of more than 112 dB SPL, all at extremely low distortion levels! This performance was not easy to achieve, and the design and fabrication of the MM-4's 4-inch driver is quite tricky.
The MM-4 quickly found a niche in a variety of applications requiring extremely low profile, yet high fidelity. The MM-4 has found a great deal of use providing front fill, sometimes mounted hidden below a stage lip in a theatre or in the steps in a church. It remains one of Meyer Sound's most popular products for fixed installation.
Loudspeaker systems commonly change their radiation pattern with frequency. This leads to uneven coverage and undesirable interactions between loudspeakers in arrays. The system described in the patent (which is the UPA-1P, though not specifically named as such) uses a combination of horn design, signal conditioning, and iterative prototyping to arrive at a design exhibiting frequency independence in the focal point.
The patent describes the system comprehensively, including the signal conditioning and arraying techniques.
These challenges were brought to John Meyer, who undertook a massive research effort in Meyer Sound's anechoic chamber to develop a new horn with lower distortion, excellent off-axis response, and highly controlled dispersion. Advanced modeling techniques were combined with many iterations of designs before Meyer finally came up with a design that met all of the needs.
This design was used in the creation of the CQ-1 and -2 loudspeakers, which were installed into the opera house in time for its reopening in September 1997. Although the CQ-1 and -2 were not released as products until 1998, within months of their use in the opera house, they were nominated for a TEC Award. A patent for the horn design (#5,925,856) was filed in 1997 and issued in 1999.
The MSL-4 worked and was well received; even today it is considered a workhorse of the industry. In fact, the success of the MSL-4 outstripped Meyer Sound's expectations, and the company soon began converting all of its products to be self-powered.
However, the challenges of making a system like the MSL-4 were considerable and, initially, some were skeptical of its practicality. Consequently, Meyer Sound stood alone in the marketplace with its self-powered systems for nearly five years before any other manufacturers took a serious stab at the technology. Even then, others have been slow to take the leap, while Meyer Sound has perfected self-powering and made converts to it around the world.
The MSL-4's cabinet design was the subject of a design patent.
John Meyer decided that the needs of the research he wanted to do required that the company have its own anechoic chamber. The chamber was built in a shed that formerly housed an old gas station, a building-within-a-building. As private anechoic chambers go, Meyer Sound's is fairly large, with anechoic response allowing measurements down as low as 80 Hz.
The room is dominated by a large mechanical arm used to hold and rotate loudspeakers in fine increments for measurements such as those done to create loudspeaker models for the MAPP Online Pro acoustical prediction program. The arm was purchased from a Colorado company that makes rotation mechanisms for astronomical observatories, the only place John Meyer could find a company accustomed to making large mechanisms that could move, under program control, in small increments with high precision. Of course, the mechanism was highly customized for Meyer Sound's needs.
The first big payoff for all the investment came in the development of new horns for the CQ series of loudspeakers. The anechoic chamber is now heavily used in development, and is the location of nearly all data acquisition for the MAPP Online Pro acoustical prediction program.
In 1992, on the 30th anniversary of the R&D awards, Meyer Sound Laboratories received an award for the SIM System II acoustic test and measurement system. Recognition for Meyer Sound, then still a small professional audio company, was a heady accomplishment and validation for John Meyer's vision.
The introduction of the original SIM system changed the face of audio measurement by employing source independent measurement, which provided much more meaningful analysis than real-time analyzers. However, the first SIM system was built around a Bruel & Kjaer dual FFT analyzer that was not entirely optimized for the job. SIM II, built from the ground up to do source independent measurement for audio, was a huge step forward, offering three DSP engines to provide three simultaneous transfer functions, multichannel operation, constant-Q FFTs, and many other advances.
The magnitude of this breakthrough was recognized when SIM II was presented an R&D 100 Award in 1992.
This award was Meyer Sound's second TEC. In this year, the Mix Foundation, a non-profit organization, was set up and took over the TEC Awards
The HD-1 was never even intended to be a product; it was designed to be an in-house test source for evaluating microphones. However, in one of audio's many legendary twists of fate, Grammy-winning engineer Roger Nichols (famed for his long association with Steely Dan, among others) visited the Meyer Sound factory, happened to hear the prototype, and relentlessly implored John Meyer to make and loan him a pair to use mixing Rickie Lee Jones's Flying Cowboys album. Things took off from there. Well over 15 years later, orders continue to be filled for the HD-1.
Originally developed to allow a SIM audio analyzer to be inserted into a sound system without deleterious effects, this patent is for an input circuit designed to avoid the injection of AC noise and provide the same gain no matter how the output feeding it is wired. The key to the circuit is that two transformers are employed in a serial, "hum-bucking" fashion such that any two of the three input pins will properly couple through one or both transformers without gain change while rejecting common-mode signals. Further, current transformers are used, rather than voltage transformers, so that the signal level passing through the transformers never reaches levels where common problems like eddy currents, ringing, phase shift, and hysteresis are encountered.
The second patent describes an improved version of this circuit that uses a single, center-tapped transformer in place of the matched pair of transformers.
By 1986, the festival was firmly established, growing steadily, and in need of better sound, so Nobs called the Meyers, who had established Meyer Sound by that time. The opportunity to help out an old friend and be the official sound sponsor for a well-respected, high-profile festival combined with the chance to try out new products in the field with a broad range of musical styles to make for an irresistible opportunity. So began the relationship between Meyer Sound and the festival, which continues to this day.
Being an entirely new measurement method, Meyer Sound gave some training classes that proved to be the beginning of what became the company's ongoing worldwide seminar series today.
Second, the UPA-1 was used with a dedicated CEU. Although the UM-1 also had a CEU, the UPA-1, which was only a year behind the UM-1, created a sensation with its performance, legitimizing for many the idea of dedicated loudspeaker processing.
Finally, there was the UPA-1's trapezoidal cabinet shape. John Meyer was espousing the benefits of point-source arrays, which were not possible to achieve with rectangular boxes. The UPA-1s trapezoidal shape allowed it to be tight-packed or splayed, but to behave as if there was a sound source emanating from behind the cabinets.
With its high output, low distortion, and small footprint, the UPA-1 had exceptionally broad applications, causing it to be widely embraced, but the theatre world, in particular, immediately began making the UPA-1 — which had been designed in part for the needs of Abe Jacobs, dean of Broadway sound designers — into a standard part of theatrical sound systems.
The MSL-10 was a high-power, high-Q system, powered by its own MS-10 amplifiers and M-10A controller, that provided 30-degree sections that could be combined into arrays to cover areas as wide as needed. One of the design goals was to prove the validity of the architecture, then create a product that broke the MSL-10 into smaller "chunks" that could be arrayed more flexibly. That product turned out to be the MSL-3
The release of the UltraMonitor marked the first time a commercially available loudspeaker was accompanied by a dedicated processor, the Control Electronics Unit, or CEU
The second CEU, for the UM-1 UltraMonitor, enabled the two-way stage monitor to generate extremely high output levels with low distortion, extended frequency response and unprecedented gain before feedback.
After one tour of the 70 mm print, however, Apocalypse went to a 35 mm release, which did not seem to present as strong a demand for a subwoofer. Meyer then showed the 650 to bassist Phil Lesh of the Grateful Dead, who immediately took an interest. Eventually, a second driver was added because the single driver had a high failure rate and the 650-R2 was born. The 650-R2 lasted until self-powering was added to make the 650-P. The 650 lineage is one of the most distinguished in the history of low-frequency reproduction.
Unfortunately, the U.S. dollar fell against the Swiss franc while this was happening and the loudspeaker he'd designed suddenly became too expensive to make for use in discos, so Meyer decided to build a studio monitor with the driver instead. Thus, the Meyer/ACD studio monitor came into being.
The ACD was a proto-self-powered system, in that it included a rack with an amplifier and processing electronics. In 1979, Meyer Sound was founded to distribute the ACD, but the price, $15,000, was extremely high for 1979, and it was difficult to sell many of them.
The ACD nonetheless accomplished two important things: first, it raised the bar for distortion and flat response in studio monitors, second, it attracted attention, which led to involvement in Francis Ford Coppola's film, Apocalypse Now, and evolution of the Meyer/ACD design into both the UltraMonitor and the UPA-1.
In 1974, economic conditions changed and the institute was forced to close.
At that time, there were no off-the-shelf loudspeakers manufactured for professional sound reinforcement. In fact, the need for such systems had just started to manifest itself in the last five years or so with the rise of the Beatles and large rock and roll concerts. Sound companies like McCune had to design and build their own equipment.
The Glyph system created enough of an impression that McCune offered Meyer a job designing loudspeakers for them. This turned out to be a fruitful relationship that produced the JM3 and JM10 systems and served as a platform for John Meyer to explore the ideas that he later brought to maturity at Meyer Sound.
Glyph Sound Systems was based on Sixth Street in Berkeley, less than a mile from Meyer Sound today. Stewart Brand featured a photo of the Glyph in The Last Whole Earth Catalog, with a caption that read, in part, "The first loud sound I've heard that didn't make me want to run. I wanted to stay and shake."
Meyer Sound Patents
From its beginning, Meyer Sound has been known as a leading innovator in performance audio products. Our list of industry firsts includes trapezoidal cabinets, dedicated loudspeaker processors, self-powered loudspeakers, source independent measurement, parabolic long-throw transducers, cardioid subwoofers, the REM manifold, Internet-enabled acoustical prediction, and more.
The technology underlying such innovations can be traced through the course of our patent history. Patents have played an important role at Meyer Sound since the company was established in 1979. Our first U.S. patent (4,152,552) was granted within weeks of the time we opened for business, and has served as a technological foundation for product development ever since.
To be valid, any claim for an intellectual (technically, “utility”) patent must mark a departure in thinking from what is generally accepted and known in the trade. But you don't have to actually make a functional device - or make anything at all, for that matter - in order to patent your idea.
At Meyer Sound, however, all our patents have been incorporated into products in some way, with tangible benefits for the professional audio community. In one sense, we use the patenting process as a framework to transform fledgling concepts into effective products. Seeking a patent disciplines our engineering team by making us more careful and thorough in our work.
Although Meyer Sound’s patent history includes several milestones in audio engineering, it doesn't tell the whole story. We haven’t sought patents on all of our new ideas. Instead we have focused our patent applications on those key concepts that define our distinctive approach to sound reproduction technology.
Arrayable loudspeaker
Country | File Date | Issue Date | Patent No. |
---|---|---|---|
JAPAN | 12/12/2017 | 10/26/2018 | 1618296 |
SOUTH KOREA | 12/12/2017 | 02/21/2019 | 30-0995433 |
Arrayable loudspeaker
Country | File Date | Issue Date | Patent No. |
---|---|---|---|
JAPAN | 12/12/2017 | 11/30/2018 | 1620892 |
SOUTH KOREA | 12/12/2017 | 02/21/2019 | 30-0995435 |
Hearing aid having level and frequency-dependent gain
Country | File Date | Issue Date | Patent No. |
---|---|---|---|
SWITZERLAND | 08/14/2013 | 03/06/2019 | 2885872 |
GERMANY | 08/14/2013 | 03/06/2019 | 2885872 |
DENMARK | 08/14/2013 | 03/06/2019 | 2885872 |
SPAIN | 08/14/2013 | 03/06/2019 | 2885872 |
FRANCE | 08/14/2013 | 03/06/2019 | 2885872 |
UNITED KINGDOM | 08/14/2013 | 03/06/2019 | 2885872 |
ITALY | 08/14/2013 | 03/06/2019 | 502019000036366 |
NETHERLANDS | 08/14/2013 | 03/06/2019 | 2885872 |
NORWAY | 08/14/2013 | 03/06/2019 | 2885872 |
SWEDEN | 08/14/2013 | 03/06/2019 | 2885872 |
UNITED STATES | 08/14/2013 | 10/06/2015 | 9,154,889 |
UNITED STATES | 08/31/2017 | 05/21/2019 | 10,299,047 |
Arrayable loudspeaker with constant wide beamwidth
Phase inversion filter for correcting low frequency phase distortion in a loudspeaker system
Magnitude and phase correction of a hearing device
Country | File Date | Issue Date | Patent No. |
---|---|---|---|
UNITED STATES | 11/24/2014 | 07/12/2016 | 9,392,366 |
Filter with independently adjustable band gain and break point slopes and method of constructing same
Loudspeaker
Country | File Date | Issue Date | Patent No. |
---|---|---|---|
CANADA | 09/16/2015 | 04/12/2016 | 164384 |
CHINA | 09/18/2015 | 05/18/2016 | ZL201530362256.2 |
SOUTH KOREA | 09/17/2015 | 07/15/2016 | 30-0864853 |
REGISTERED COMMUNITY DESIGN | 09/17/2015 | 09/17/2015 | 002774000-0001/000 |
Loudspeaker
Loudspeaker
Arrayable loudspeaker
Loudspeaker
Country | File Date | Issue Date | Patent No. |
---|---|---|---|
CHINA | 03/02/2016 | 11/23/2016 | ZL201630057583.1 |
SOUTH KOREA | 03/02/2016 | 01/06/2017 | 30-0890083 |
REGISTERED COMMUNITY DESIGN | 03/01/2016 | 03/01/2016 | 003008465-0001 |
Dynamic acoustic control system and method for hospitality spaces
Loudspeaker rigging system having upwardly extending connecting links
Country | File Date | Issue Date | Patent No. |
---|---|---|---|
BELGIUM | 08/16/2012 | 11/02/2016 | 2744370 |
CANADA | 08/16/2012 | 10/23/2018 | 2,845,595 |
SWITZERLAND | 08/16/2012 | 11/02/2016 | 2744370 |
CHINA | 08/16/2012 | 07/06/2016 | ZL201280050677.5 |
GERMANY | 08/16/2012 | 11/02/2016 | 2744370 |
DENMARK | 08/16/2012 | 11/02/2016 | 2744370 |
SPAIN | 08/16/2012 | 11/02/2016 | 2744370 |
FRANCE | 08/16/2012 | 11/02/2016 | 2744370 |
UNITED KINGDOM | 08/16/2012 | 11/02/2016 | 2744370 |
HONG KONG | 08/16/2012 | 06/09/2017 | HK1196234 |
IRELAND | 08/16/2012 | 11/02/2016 | 2744370 |
JAPAN | 08/16/2012 | 09/02/2016 | 5998219 |
LUXEMBOURG | 08/16/2012 | 11/02/2016 | 2744370 |
NETHERLANDS | 08/16/2012 | 11/02/2016 | 2744370 |
NORWAY | 08/16/2012 | 11/02/2016 | 2744370 |
SWEDEN | 08/16/2012 | 11/02/2016 | 2744370 |
Acoustically absorptive panel
Country | File Date | Issue Date | Patent No. |
---|---|---|---|
UNITED STATES | 05/11/2012 | 01/28/2014 | 8,636,104 |
Cooling system for loudspeaker transducers
Filtering system for equalizing a loudspeaker system
Integrated rigging system for loudspeakers with vertically and horizontally oriented locking pin holes and dolly board placed in abutment with adjacent dolly boards
Loudspeaker with passive low frequency directional control
Country | File Date | Issue Date | Patent No. |
---|---|---|---|
CHINA | 03/19/2010 | 09/17/2014 | ZL201080020139.2 |
HONG KONG | 12/01/2014 | 05/15/2015 | HK1169254 |
MEXICO | 09/19/2010 | 09/18/2013 | 313362 |
Circuit and method for reducing noise in class D amplifiers
Country | File Date | Issue Date | Patent No. |
---|---|---|---|
CANADA | 10/19/2010 | 11/07/2017 | 2,815,315 |
CHINA | 06/11/2012 | 01/13/2016 | ZL201080056261.5 |
Loudspeaker system with extended constant vertical beamwidth control
Loudspeaker system and method for producing synthesized directional sound beam
Loudspeaker
Loudspeaker
Loudspeaker grille
Loudspeaker rigging system having contained maneuverable connecting links
Country | File Date | Issue Date | Patent No. |
---|---|---|---|
UNITED STATES | 01/13/2005 | 12/15/2009 | 7,634,100 |
Loudspeaker horn
Loudspeaker
Country | File Date | Issue Date | Patent No. |
---|---|---|---|
REGISTERED COMMUNITY DESIGN | 04/09/2009 | 04/09/2009 | 1120307-0001-0002 |
Loudspeaker horn and method for controlling grating lobes in a line array of acoustic sources
Loudspeaker
System and user interface for producing acoustic response predictions via a communications network
Country | File Date | Issue Date | Patent No. |
---|---|---|---|
UNITED STATES | 09/24/2001 | 05/17/2005 | 6,895,378 |
Microphone
Microphone
Frequency dependent excursion limiter
Front of a loudspeaker
Manifold for a horn loudspeaker and method
Country | File Date | Issue Date | Patent No. |
---|---|---|---|
CHINA | 09/09/2003 | 06/11/2008 | ZL02806221.3 |
Rigging system for loudspeakers
Country | File Date | Issue Date | Patent No. |
---|---|---|---|
SWITZERLAND | 02/20/2002 | 04/27/2011 | 1369005 |
SPAIN | 02/20/2002 | 04/27/2011 | 1369005 |
FRANCE | 02/20/2002 | 04/27/2011 | 1369005 |
UNITED KINGDOM | 02/20/2002 | 04/27/2011 | 1369005 |
HONG KONG | 12/22/2003 | 11/25/2011 | HK1056965 |
ITALY | 02/20/2002 | 04/27/2011 | 502011901965326 |
Loudspeaker system with feedback control for improved bandwidth and distortion reduction
Arrayable two-way loudspeaker system and method
Loudspeaker horn
Broadband acoustical transmitting system
Method and circuit for improving the polar response of a two-way horn-loaded loudspeaker system
Multiple tuned high power bass reflex speaker system
Loudspeaker
Country | File Date | Issue Date | Patent No. |
---|---|---|---|
GERMANY | 09/06/1995 | 11/21/1995 | M9507071.0 |
FRANCE | 09/07/1995 | 03/14/1997 | 954834 |
HONG KONG | 08/08/2005 | 9802016.3 |
Loudspeaker
Acoustical ranging transceiver
Correction circuit and method for improving the transient behavior of a two-way loudspeaker system
Country | File Date | Issue Date | Patent No. |
---|---|---|---|
UNITED STATES | 07/18/1991 | 02/09/1993 | 5,185,801 |
Ohmically isolating input circuit
Ohmically isolated input circuit
Circuit and method for correcting distortion in a digital audio system
Country | File Date | Issue Date | Patent No. |
---|---|---|---|
EUROPEAN PATENT CO | 10/24/1983 | 10/31/1984 | EP0122939A |
JAPAN | 06/25/1984 | 08/16/1988 | JPS59501930A |
Loudspeaker enclosure
Loudspeaker
Horn speaker and method for producing low distortion sound
Country | File Date | Issue Date | Patent No. |
---|---|---|---|
FRANCE | 02/01/1978 | 01/22/1986 | 2,379,220 |
UNITED KINGDOM | 03/20/1978 | 03/20/1978 | 1591480 |
JAPAN | 02/01/1978 | 05/01/1979 | JPS53102024A |
The Self-Powered Advantage
Meyer Sound has been pioneering self-powered loudspeakers for professional installations and touring since 1995. We’ve committed to self-powered systems because we know they deliver unrivaled clarity, reliable performance, value, and ease of use.
If you’ve been thinking about investing in a self-powered system, you’ve come to the right place.
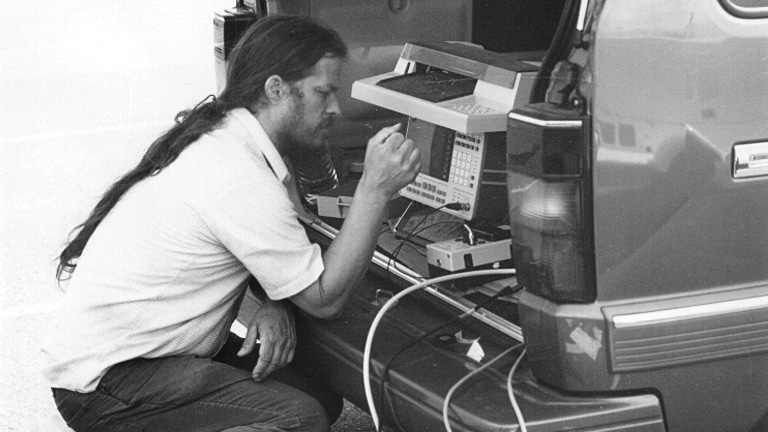
First, a Little History...
The story of self-powered loudspeakers is in many ways the story of Meyer Sound itself.
In the 1970s, sound reinforcement technology was inconsistent science at best, and at worst, led to show-ending failures. A young John Meyer, designing loudspeakers for San Francisco’s McCune Sound Service, wanted to bring quality and reliability to sound systems, and he knew the answer lay in self-powered loudspeakers. In 1979 Meyer founded his own speaker company; early Meyer Sound innovations include the iconic HD-1 self-powered studio monitor launched in 1989.
Today Meyer Sound offers a full range of self-powered sound reinforcement products. Meyer Sound systems can be found on tour with artists ranging from Ed Sheeran to Metallica, on Broadway and London’s West End, and in performance venues from the San Francisco Opera to the Vienna Philharmonic not to mention sports stadiums, cruise ships, and houses of worship around the world.
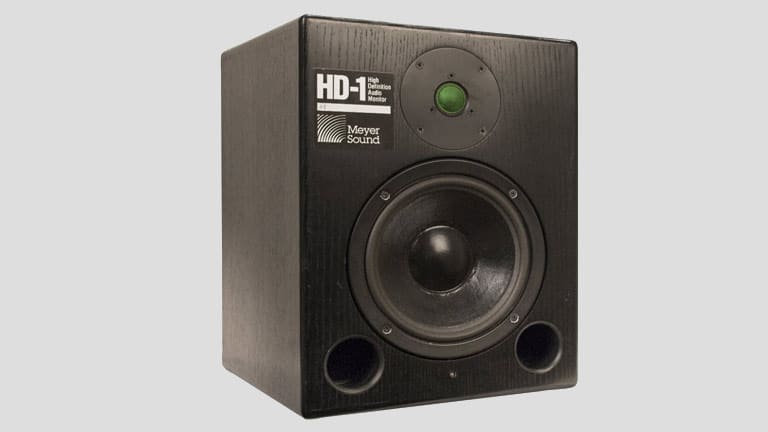
Why Self-Powered?
Self-powered loudspeakers offer several advantages over their passive counterparts when it comes to fidelity, reliability, and simplicity. The great part is, you’ll start to reap the benefits of a self-powered system before you even power up.
Ease of deployment: System set-up is so much easier when you have fewer components and fewer cables to worry about being miswired. Since self-powered loudspeakers incorporate amplification, you’ll never have to deal with matching speakers to amplifiers or connecting components. You don’t have to worry about calibration of gain and crossover setting which means more time focusing on the show. Eliminating amp racks doesn’t just streamline system deployment, it streamlines your inventory whether you’re a rental house or a road warrior. And when you consider that the average amp rack weighs nearly 300 pounds and takes up four feet of truck space, the efficiencies get even clearer. Let alone when you want to fly the amplifier racks to get closer to the speakers, often requiring more rigging points and more motors.
Predictable, reliable operation: Internal amplification is closely matched to drivers. Because individual components have been optimized during manufacturing, you can expect consistent sound from show to show. Built-in, factory-optimized protection circuitry provides extra assurance without degrading signal quality. And, when you have less equipment, you have less risk of failure.
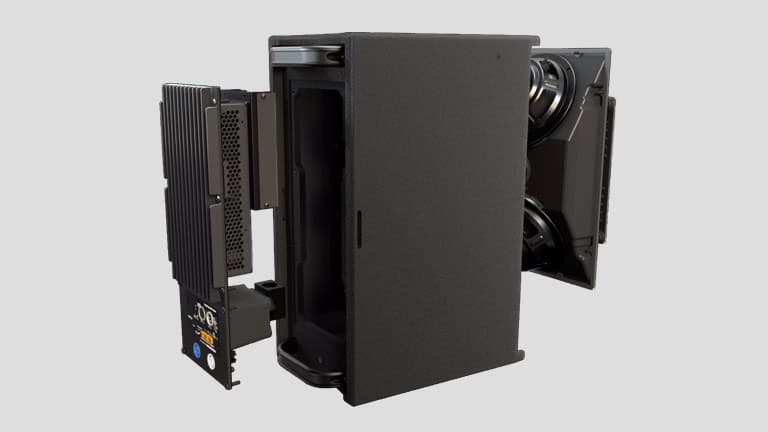
Better frequency and phase response: Because self-powered loudspeakers incorporate sophisticated processing, they are calibrated to exhibit optimal response curves in key performance parameters. Active crossovers are more precise, sophisticated designs, and bi-amped systems are time aligned, eliminating phase issues. The result? Accurate sound throughout the speaker’s range, at any volume level.
Unparalleled clarity: In powered monitors, internal amplifiers are precision-matched to drivers, delivering optimal power at all times for cleaner sound. And because amps are built into loudspeaker cabinets, there’s no need for long lengths of connecting cable, which can become prone to distortion and signal loss.
Tighter transients: Since self-powered loudspeakers have very short internal cables, amps inside can more effectively dampen driver mechanical motion, which leads to better sonic accuracy and tighter, crisper transients. (And, there’s none of the loss in levels and signal quality inherent over long cable distances.)
Certified Safe: Nothing matters more than the safety of your staff and customers. Because self-powered loudspeakers incorporate amplification, they must undergo rigorous testing by Underwriters Laboratories and other international organizations to ensure they operate safely and guard against the risk of fire, electric shock, and inadequate structural design. Enjoy peace of mind knowing Meyer Sound powered products are certified by FCC, UL, CSA, CE, and CEE the most stringent agencies in the business.
The Problems with Passive
What about passive loudspeakers? At first glance, passive systems may seem like a bargain. But we already know that passive systems require more components and accessories than powered systems. Sonically, they exhibit potential for signal loss over distances, and it is very hard to ensure consistent, optimal sound and volume as amplifiers have many variables to consider when being matched to loudspeakers, such as cable lengths and gauge as well as the number of speakers connected to the amplifier.
Passive systems are often touted as easy to service. But because powered loudspeakers are so complex to design and build, self-powered loudspeakers usually represent the top innovations from leading manufacturers. Better quality translates to better reliability, which means fewer maintenance issues in the long run.
At face value, passive systems might seem less expensive and easier to maintain. But once you start adding in amps, cables, and other components not to mention increased transport and labor costs you’ll find that those savings just don’t add up to a better value.
Step Up to a Self-Powered System
Once you recognize all of the advantages inherent in self-powered loudspeaker systems, it’s easy to understand why the world’s top venues and productions rely on them to deliver consistently stunning sound.
About Us
Creating extraordinary sound experiences is the essence of what we do — from the arena-quaking thunder of Metallica to the immersive thrills of Cirque du Soleil. At Meyer Sound, we continually strive to elevate the dialogue about sound and cultivate a greater awareness of the importance of how we hear and listen.
Founded in 1979 by John and Helen Meyer, our company is globally recognized as a leader in integrated sound reinforcement solutions. Meyer Sound systems can be heard on tour with artists like Ed Sheeran, Sigur Rós, Post Malone, and Celine Dion; at iconic venues including Jazz at Lincoln Center, the Cologne Philharmonic Hall, the Montreux Jazz Festival, and Cirque du Soleil’s Las Vegas productions; along with theatres, cinemas, arenas, houses of worship, restaurants, theme parks, and museums around the world.
Our products are designed and hand-crafted at our Berkeley headquarters, with offices and distributors around the globe. Our work has generated more than 100 patents and numerous industry awards, including TEC, MIPA, and Eddy Awards, and the prestigious R&D 100 Award.
Philanthropy
We are company that firmly believes in giving back and we instill that value into everything we do. Founders John and Helen Meyer have been deeply involved in the Bay Area arts community for decades. We support arts institutions and philanthropic organizations throughout the San Francisco Bay Area, including the San Francisco Opera, Cal Performances, and The UC Theatre. Helen Meyer has worked tirelessly to empower individuals and enrich the local community in the areas of job creation, education, and philanthropy, serving on the boards of Cal Performances, the San Francisco Opera, and the Mark Morris Dance Group.
Our Culture and Benefits
A collaborative, results-focused approach to sound solutions drives a company philosophy where creative thinking, old-fashioned craftsmanship, and entrepreneurial technology are strongly intertwined.
At Meyer Sound you will help create world-class products and technologies; you’ll do your best work, cultivate your passion, and make your mark. This isn’t just a job, it’s a career. The average tenure here is ten years and many of our employees have been with us for much longer.
We’ve built a vibrant culture that fosters professional excellence in an environment that truly delivers work/life balance. Full-time employees enjoy a generous compensation package which includes:
- Paid time off
- Comprehensive health, dental, vision benefits
- 401K plan
- Life/Long-term disability insurance
- Generous parental leave
- IDShield identity protection
- Wellness and commuter benefits
- Employee parties and movie nights
- Pet insurance
- Dog-friendly environment
Internships
We offer a summer internship program that aims to provide hands-on experience and help you build skills which can lead to outstanding career opportunities:
- Summer internships run June through August
- The internship application process begins in February
- Candidates must currently be enrolled in an accredited undergraduate or graduate program or have graduated within one year
- Internships are available in Design Services, Technical Support, R&D, Marketing, Manufacturing, and Quality Control
Careers
We love working with people who have a passion for audio and understand the value of sound. If this describes you, please explore our employment opportunities.
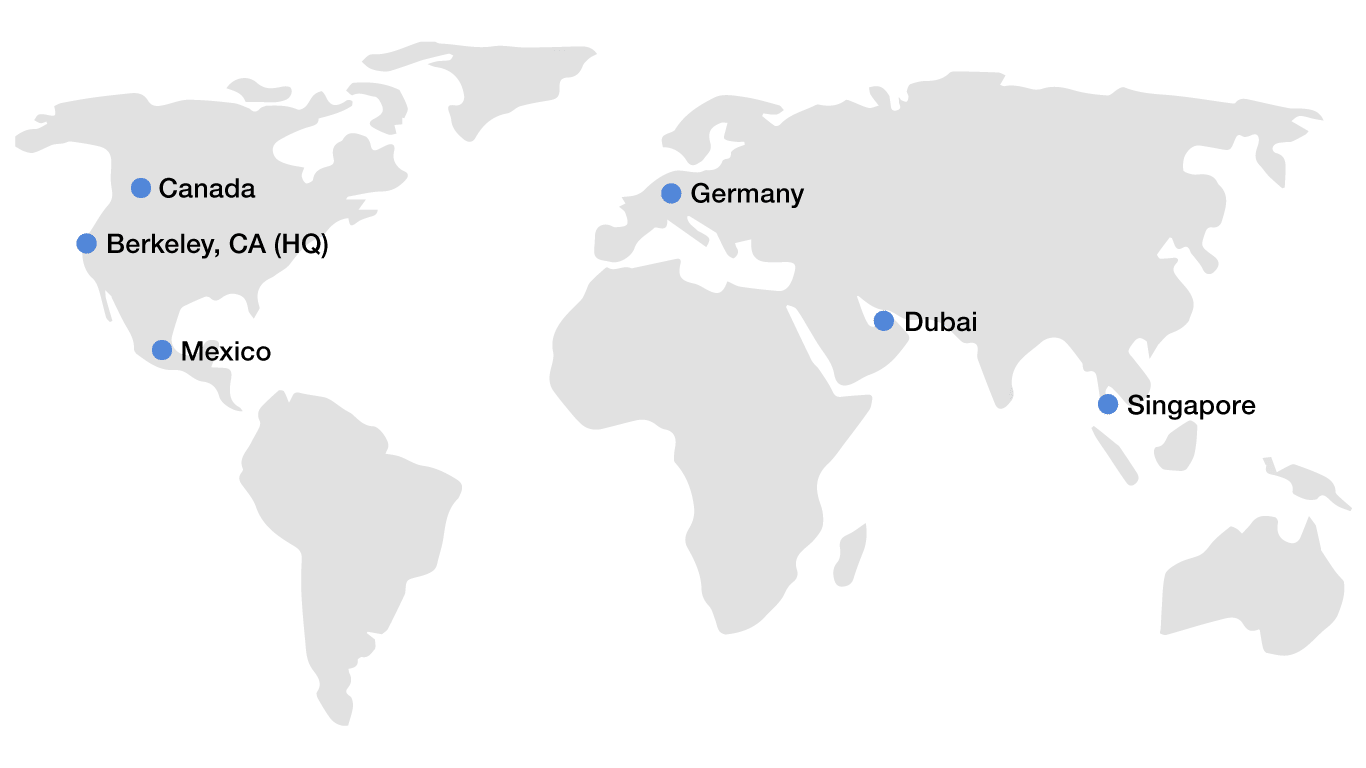